動力を用いるおよそあらゆる機械に、なくてはならない部品であるギヤ。
歯車一枚一枚に込められた工夫が、社会の発展を下支えしている。
歯車を組み合わせて力を操る
1949年に発行された五円硬貨には、戦後日本の発展を願って、主な産業がデザイン化された絵が刻まれている。頭を垂れる稲穂は農業を象徴、下部の水平な線は文字通りの水平線で、水産業を象徴。中心の穴を縁取るように描かれているのは歯車で、工業の象徴として描かれた。
歯車は英語でギヤという。日本語では歯車という言葉が浸透しているため、ギヤというと複数の歯車が組み合わされた仕組みのことを思い浮かべがちだが、歯車を組み合わせた仕組みは正確にはギヤボックスと呼ばれる。
日本銀行の五円硬貨のデザインを待つまでもなく、ギヤはおよそあらゆる機械に使われ、工業にはなくてはならない部品として長く活用されてきた。一説には、ローマ時代から用いられていたという。一枚だけではギザギザのついた円盤にすぎないが、複数枚を組み合わせたり、同じ歯の形状を持つ他の部品と組み合わせることで、運動のスピードと力の方向、強さを自在にコントロールして伝えることができる。
例えば、歯の数が100のギヤと50のギヤを組み合わせたとしよう。そうすると、100のギヤが1周回る間に、50のギヤは2周する。回転運動の速さが2倍になったわけだ。反対に50のギヤに力を加えて一周させたときは、100のギヤは半周しか回らない。しかし、このとき50のギヤに加えた力は失われたわけではなく、2倍の力(トルク)で100のギヤを回している。これこそギヤの真髄ともいえるもので、減速機構という呼び名で、大きなトルクが必要となるさまざまな場面で用いられている。
その恩恵を最も身近に感じられるのが自動車のトランスミッションで、一秒間に数千回転というエンジンの運動を、「減速」することで、大きなトルクを生み出している。1トンを超える自動車がスムーズに発進できるのはこのおかげだ。
小さいものでは腕時計に1ミリを切るようなサイズのギヤが使われ、大きいものでは船舶や風車に数メートルもの巨大なギヤが内蔵されている。産業用の大型機械にとっても動力源の力の強さとスピードを自在に操れるギヤは不可欠だ。車輪は人間が生み出した最大の発明だといわれることがあるが、ギヤもそれに負けず劣らず重要な発明だったといっても決して言い過ぎではない。
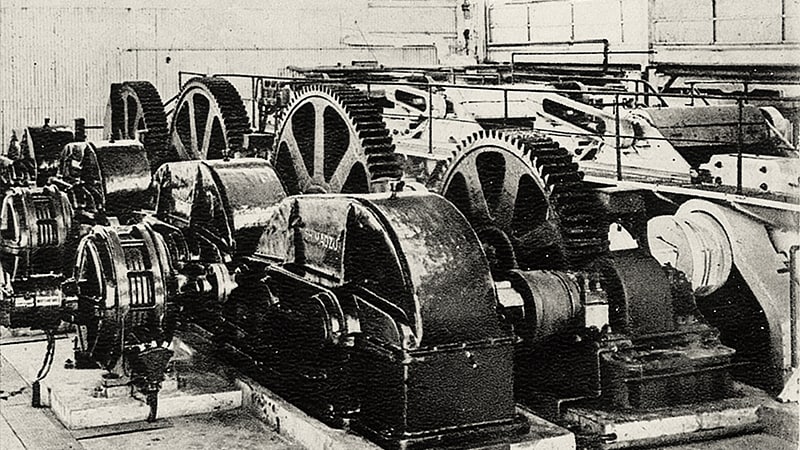
ギヤはあらゆる工場で、産業機械の力とスピードをコントロールするために使われた。
航空機用ギヤの製造は職人技のオンパレード
およそすべての工業製品の中で、最も高い技術力が求められるものの一つが航空機だろう。重力に反して巨大な金属の塊を空高く舞い上がらせるためには、部品の一つひとつにいたるまで徹底した軽量化が求められる。しかも、装置の故障や部品の破損は、事故に直結するため、頑丈さも決して手を抜くことはできない。
もちろんギヤも例外ではない。航空機エンジンが発生する高速な回転運動を、大きな機体の各所にある機構に分配するために、航空機には約1000点ものギヤで構成された大小さまざまなギヤボックスが搭載され、その一点一点に軽さと頑丈さを高める工夫が施されている。
軽量化するためには、小さく薄くすればいい。しかし薄くすればするほど必然的に頑丈さは失われていく。強度が足りないところに無理な力がかかると、歯車の歯が変形してしまうこともある。接触する表面には十分な硬さが求められるが、歯車全体に硬い材質を使ってしまうと、もろくなってしまい、歯車そのものが割れてしまうということにもなりかねない。
そこで用いられるのが、浸炭処理という技術だ。表面層に炭素を添加して、焼き入れ・焼き戻しを行うことで、歯同士が接触する表面を十分に硬くする。一方、表面以外は元の鋼材の性質を保っており、ほどよい柔らかさで衝撃を受け止める。炭素を添加しやすく適度な硬度を持つ鋼材選びや表面硬化手法の改良は、航空機用ギヤ開発の一丁目一番地だ。
一方、加熱と冷却を行うと、歯車にはどうしても歪みが生じてしまう。もちろん、設計通りの力を発揮させるためには、歯の精度には寸分の狂いも許されない。そこで、浸炭処理を行ったあと、一点一点磨いて形を補正する。まるで工芸品のような手間が、航空機用ギヤには求められるのだ。
国産初の旅客機にも採用された島津のギヤ
島津製作所は、大正期に産業機械用の減速装置「ギヤカップリング」を生産。当時、動力源から作業機械へ動力を伝達したり回転数を変換するには、もっぱらベルトが用いられていたが、ギヤを担当する島津の営業スタッフは、日本各地の工場をめぐっては伝達効率に優れていることや速度変換が確実であることなど、メリットを説いて回ったという。一方、昭和初期には航空機事業に参入。油圧機器類や気化器などを生産した。
この2つの事業における経験、知見が融合して生まれたのが航空機用ギヤボックスだ。1955年、国の航空機事業再開プランに合わせて島津もさまざまな機器の製造を開始。1957年、本格的な事業化を目指して航空機事業部を設立し、1961年には国産初の旅客機YS-11のフラップ(高揚力装置)のギヤボックスを担当。日本の翼の初フライトに一役買った形だ。
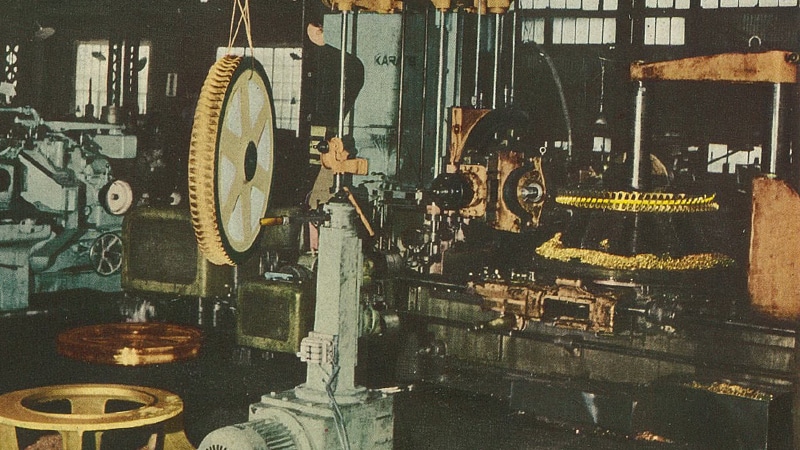
その後もボーイング社のジャンボジェットのフラップ用ギヤボックスなどを担当。求められる要件に合わせ、ギヤボックスの設計から、歯車一枚一枚の製造、組み立てまでトータルで引き受けられる稀有な企業として信頼を勝ち得ている。
近年、ギヤボックスは、軽さや頑丈さだけでなく、動力の伝達効率を高める方向へと進化しつつある。一見スムーズにかみ合っているように見えるギヤボックスにおいても、ミクロ的には歯車と歯車の間では絶えず転がりと滑りを繰り返しており、この滑り運動が摩擦損失となりどうしても力の伝達ロスが発生する。理論上は2の力が伝えられるよう設計しても、組み立ててみると、1.7程度しか伝えられないのは織り込み済みで、その分ギヤボックスに入力する力を大きくすることで、フラップなどの動作に必要な力を確保してきた。
しかし、空においても省エネルギーを求める声は高まっており、島津は歯の形状を工夫することで、伝達ロスを最小化するギヤボックスを航空機メーカーに提案している。
グローバル化の進展で航空機需要が一層高まるなか、ギヤへ注がれる目もさらに熱を帯びている。
※所属・役職は取材当時のものです
記事検索キーワード
VOL.40その他の記事
-
VOL.40震災を機に転換期を迎えた福島の農業
地元待望の農学部が果たす重要な役割とは? -
VOL.404次元像から立位CT撮影、AIの活用
患者に優しい医療を支える画像診断の未来 -
VOL.40持続可能な社会のために必要な素材として期待される世界初の生分解性ポリマーの開発
-
VOL.40時計から航空機まで、あらゆる動力源の力の強さとスピードを自在に操る
社会の発展に必要不可欠なギヤの魅力 -
VOL.40生き物はみな腸内細菌のおかげで生きている!?
「うんちハンター」の異名を持つ生化学者の冒険譚 -
VOL.40どこからがパワハラなのか…
あいまいな境界線を見極め、組織のコミュニケーションを円滑にする -
VOL.40患者さんにも技師にも優しい“SHIMADZU”を
院内での安全性、使いやすさ、デザイン性という高い期待に応えた回診用X線撮影装置の開発 - NEWS & TOPICS2018年9月~2019年3月
-
- 2018.12.4第38回(平成30年度)島津賞 京都大学 化学研究所 金光義彦氏に
- 2019.2.15四重極飛行時間型質量分析計LCMS-9030™がiF DESIGN AWARD 2019を受賞
- 2018.8.22汎用医療用X線装置ダイアナ号が未来技術遺産に登録