1980年代"産業のコメ"という二つ名をとった半導体。日本は世界トップレベルの高性能な半導体を製造し、長くアメリカが君臨していた半導体業界の覇権を握った。技術の進化を実現した力となったのは、真空を作り出す「ターボ分子ポンプ」だった。半導体製造の転換期を支えた、島津製作所製ターボ分子ポンプの歴史を振り返る。
世界を変えたありふれた元素
純度99.999999999%。俗に〝イレブンナイン〞と呼ばれる。半導体製造に関わる人にとってはなじみ深い数字だ。
ケイ素(元素記号:Si)は半導体の土台となるシリコンウェハの素材である。ごくわずかでも不純物が混じると、半導体としての性能を損なう恐れがあるため、シリコンウェハはイレブンナインを徹底しなくてはならない。実に1000億個のケイ素原子の中に不純物の原子が1個だけしか許されないという、気の遠くなる数字である。
1960年代、アメリカにおいてケイ素を原料にしたシリコン製の半導体の工業化が確立。シリコンを薄く延ばしたシリコンウェハ上に、複雑な回路図を描くことで、集積回路(IC)やLSI、コンピュータの頭脳であるCPU、メモリなどが生み出されていった。
ケイ素は地球上で2番目に多い元素だ。大量に存在する上に高純度化しやすいことから、世界の情報化を劇的に推進させる立役者となった。
今やスマートフォン、パソコン、テレビ、冷蔵庫、自動車、航空機、銀行のATMなど、電気を用いるあらゆる機械製品には、100%シリコン由来の半導体製品が用いられている。半導体なしに現代生活は成り立たないと言っても過言ではないだろう。
半導体製造に不可欠な『 真空 』
日本は半導体関連分野で長く世界の最先端を走ってきた。特に80年代に入ってからの飛躍は顕著で、1986年には世界の半導体市場におけるシェアでアメリカを抜き去り、第一位に躍り出る。半導体供給メーカーのトップ10のうち、6社が日系企業だったというから、いかに世界を席巻したのかがうかがい知れる。
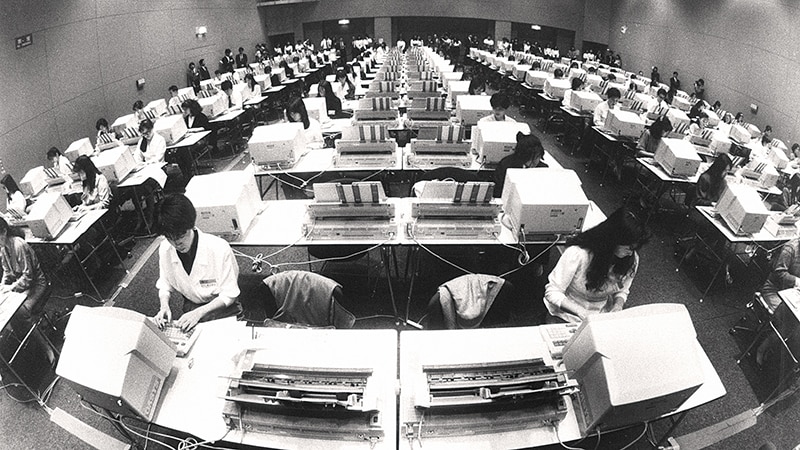
その80年代、半導体製造は一つの転換期を迎えていた。ICやLSIの高集積化により、さらなる微細化が求められるようになったのだ。そのためにはイレブンナインを保てる特別な製造環境が欠かせないものとなる。
シリコン上に回路を焼き付けるエッチングという工程では、かつて薬液でウェハ表面に蒸着させた金属の膜を腐食させる方法が取られていた。大量に処理でき、安価というメリットがあったが、腐食させるという性質上、微細加工をしようとすると、必要以上に金属膜がえぐれてしまうというデメリットも抱えていた。そこで考えられたのが、ドライエッチングという技術だ。シリコンウェハ表面の金属膜と反応性の高いガスを、ほぼ不純物が存在しない乾いた空間―すなわち『真空』にしたチャンバーと呼ばれる密閉空間内で反応させることで、高い純度と精度を持った半導体を実現させた。
実は島津と真空のかかわりは非常に古い。創業以来の得意分野たるX線装置に真空が必要だったことから、真空技術を伝統的に育んできたのだ。日の出の勢いの半導体製造からその真空技術が求められ、島津は名乗りを上げた。
1980年、真空ポンプの一つ「ターボ分子ポンプ(TMP)」をリリース。以降、半導体製造装置のコンポーネントの一つとして、世界トップ集団につけていた日本の装置メーカー各社に提案していった。
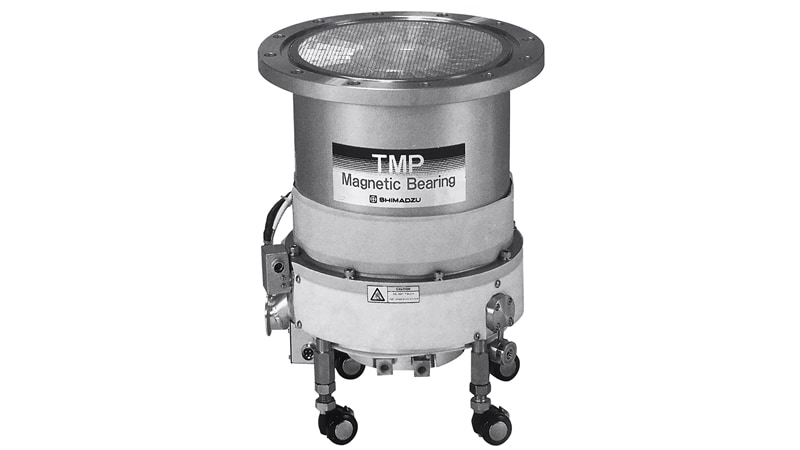
ターボ分子ポンプTMP-2001 LME
TMPはジェット機のタービンのような翼を毎分2万〜3万回転という超高速で回転させることにより、空気分子を叩き落としていく装置。瞬時に大量排気が実現するため、高度1000㎞に相当する宇宙空間なみの、超高真空を作り出すことが可能だ。要求レベルの高い半導体業界では早くからTMPが着目されていた。
同業他社の多くはTMPの高速回転を支えるのにボールベアリング型を採用していた。一方、島津では1985年、動翼の軸を電磁石の制御によって浮上させる磁気軸受型をいち早く開発することで差別化を図った。
常に技術を高め続ける
実はボールベアリングは、TMPの最大の弱点とされてきた。敵はチャンバー内の熱だ。
ドライエッチングの工程でTMPは2つの役割を果たす。一つは反応前に不純物となる空気をチャンバー内から排出すること。もう一つは金属膜と活性ガスの反応によって発生したガスを排出することだ。この時、チャンバー内のガスはかなりの高温になっているが、TMPは室温のまま。そのため、チャンバーからTMPに移ったガスは圧縮され、固体化してしまっていた。稼働させるたびに、この固体がTMP内に堆積していき、導入から3ヶ月もすればまともに動かなくなる事態に現場は頭を悩ませていたのだ。
TMPをチャンバー内と同じ温度に上げれば固体となるのは防げる。理屈の上ではそうだが、高温下では、軸受の玉や軌道に塗布されている潤滑油やグリースが蒸発し、安定した稼働が見込めなくなってしまうのだ。
こうした問題を一気に解決する手段として島津が提示したのが、タービンを支える主軸にボールベアリングを用いず、磁気軸受にするというアイデアだった。これならば高温でも対応でき、オイル類の混入も防いでくれる。島津は磁気軸受の優位性を前面に押し出して、国内大手半導体製造装置メーカーの信頼を一身に集めた。
折しも80年代半ばから90年代にかけてシリコンウェハのトレンドが直径150ミリから200ミリにスケールアップ。半導体製造装置の大幅な刷新が行われていた。そこにチャンスを見た島津は精力的に技術革新に取り組んだ。1990年には当時では最高の排気量2000リットル/秒、温度70度に対応した磁気浮上・ヒータ付きのTMP-2001LME形を開発した。
この高性能のTMPの後継機は、のちに海外にも展開されていくことになる。ご存知の通り、1990年代以降、アジア各国の新興企業が半導体業界に進出、群雄割拠の様相を呈していく。島津は97年からシリコンバレーに拠点を置き、営業活動を実施、北米の大手半導体製造装置メーカーとの取引を展開していった。
2008年には三菱重工業からTMP部門を譲り受け、国内においても事業の裾野は拡大。結果、世界的なシェアも磁気軸受型TMPでは30%台に拡大した。
現在、シリコンウェハのサイズは300ミリ時代が続いているが、近い将来、一気に450ミリに突入する可能性があるといわれている。半導体製造に用いられる物質も増加して、TMPの温度も100度を超えるスペックが要請されているという。それを支えるTMPの排気量も5000リットル/秒と、1990年の2.5倍に達している。
IoTやAIの加速度的な進化により、各デバイスに用いられる半導体の高度化は今なお至上命題だ。TMPが作り出す真空空間は、これらからも胸高鳴る未来を創造してくれるに違いない。
※所属・役職は取材当時のものです
記事検索キーワード
VOL.37その他の記事
-
特集国民的女優の運命を変えた意外なきっかけ
沢口靖子が追い求める「魂の表現」とは? -
VOL.37隕石衝突が生命の起源?
地学研究者が見つけた有機物誕生のストーリー -
VOL.37シェア可能な研究空間が生み出すイノベーション
装置を共有するメリットに迫る -
VOL.37生きるための「形」を。
乳がん患者の葛藤によりそう医師の姿勢 -
VOL.37デジタル立国日本の影の立役者
半導体製造を飛躍的に前進させたTMPとは -
VOL.37「ミドリムシで世界を救う」
ユーグレナ・出雲社長が歩んだ10年の道のり -
VOL.37「経験学習」で育て上手な上司に社内の人材育成に重要な3つの要素
-
VOL.37「世界一使いやすいガスクロを作ろう」
家電に負けない分析装置を生んだ開発者たち -
- NEWS & TOPICS2017年2月~8月
-
- 2017.2.28 / 3.232016年度なでしこ銘柄/健康経営優良法人~ホワイト500 ~に選定
- 2017.6.29チェコのソボトカ首相が来社聖アンズ大学附属病院と共同研究で調印
- 2017.3.13島津中国質量分析センターが「iF DESIGN AWARD 2017」を受賞