カーボンニュートラルを目指したグリーン成長戦略が日本政府によって策定され、2030年に温室効果ガスを2013年度から46%削減する目標が掲げられています。温室効果ガス削減目標の達成に自動車の電動化は重要な要素とされています。自動車の電動化では主要部品がモーター、バッテリーならびにインバータなどに置き換わるため、これらの急激な生産拡大に対応する生産技術改革が喫緊の産業課題となっています。特に、電気伝導性、熱伝導性が高いため電動化で多用される純銅材や軽量化を目的としたモーター用の線材需要が高まっているアルミニウムの加工需要への対応が必要不可欠とされています。ここでは青色半導体レーザによる光源、加工例ならびに分析計測装置を用いた加工品質の評価例を紹介し、将来のプロセスインフォマティクスへの展望を示します。
近年の青色半導体レーザ素子単体の高効率化、高出力化技術は目覚ましく進歩していますが、素子単体での出力は10Wに満たず、レーザ加工用光源としては出力が足りません。島津製作所では大阪大学の塚本雅裕教授らとともに2016年度からNEDOプロジェクトに参画し、多数の青色半導体レーザ素子出力を束ねる独自の高輝度ビームコンバイニング技術を用い高輝度・高出力を両立する青色半導体レーザ光源を開発してきました(表1)。2020年には500W青色半導体レーザ3台を結合するコンバイナを開発し、出力1.5kW/ファイバコア径Φ400μmを達成しています。
年度 | ファイバ出力 [W] | ファイバコア径 [μm] | パワー密度 [MW/cm2] | 備考 |
---|---|---|---|---|
2016 | 100 | Φ100 | 1.3 | |
2018 | 200 | Φ100 | 2.6 | |
1k | Φ400 | 0.8 | 200W、5台のコンバイナ出力 | |
2019 | 500 | Φ200 | 1.6 | |
2020 | 1.5k | Φ400 | 1.2 | 200W、3台のコンバイナ出力 |
課題
自動車の電動化で需要が高まる銅やアルミの加工においては、従来のレーザ加工方法から、技術開発が進む青色半導体レーザ加工へのスムーズな移行が必要になってきています。これまでのレーザ加工は技能継承による経験的ノウハウで調整されてきました。一方で、青色レーザによる加工は新たな分野であり、経験の蓄積には時間を要します。とはいえ、進行している自動車の電動化に対応するためには、経験に依存しない生産技術改革が強く求められており、喫緊の課題になっています。
ソリューション
プロセスインフォマティクスは、プロセス全体におけるデータの収集、解析を行い、最適化への活用に焦点を当てたアプローチに関する方法論や技術を意味します。レーザ加工におけるプロセスインフォマティクスでは、レーザビームパラメータや材料の物性データ、加工評価データなどを収集し、それを活用して最適な加工条件や品質向上を目指します。また生産性の向上やコスト削減にも貢献することが期待できます。
さらにデータの収集や解析、モデリング、制御には機械学習などの人工知能の技術が活用され、より進化していくことになります。
島津製作所はレーザ技術とともに金属材料の分析計測技術を有しております。この分析計測技術を用いて取得する加工品質データとレーザ加工パラメータデータを蓄積し、機械学習などのインフォマティクスを活用することで、経験に依らず、最適な加工条件を事前に予測し、プロセス開発期間を短縮することが可能になるのではないかと考えています。
以下に青色半導体レーザ光源を用いた加工とその品質の検証事例を示します。
青色半導体レーザ光源での加工と加工品質の検証事例
① EVモーター用コイルの突合せ溶接ならびに線材溶接
図1は、EV向けモーター用コイルに用いられる線材であるΦ1.8mmの純銅単線の切断面を突合せ溶接した例です。加工条件はレーザ出力1.5kW、照射ビーム径600μm、レーザ照射時間0.1sであり、酸化抑制のためにArガスを25L/minで照射部に吹き付けています。
レーザ照射により銅線が一体化され、接合部を含む銅線の電気抵抗を測定した結果、理論値と1%以下の精度で一致しており、電気的に銅単線とそん色のない性能であることを確認しています。
図2は、モーター用の線材として需要が高まっているアルミニウムの平角線の溶接例です。先端の被覆を剥がしたアルミニウム平角線(2mmx3mm)を端面が並ぶように配置し、端面にレーザを照射しています。
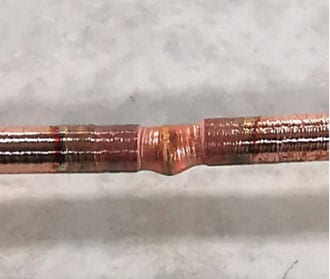
【 図1 Φ1.8mm純銅単線の溶接例 】
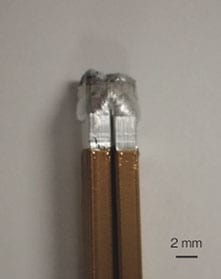
【 図2 アルミニウム平角線の溶接例 】
銅やアルミニウム材の加工プロセスを従来プロセスからレーザ溶接へスムーズに移行するためには、レーザ溶接の加工品質を正確に検証することが必要不可欠です。特に溶接内部のボイド(空隙部)は接合強度に影響を与えるため定量的な解析が必須です。
島津製作所のマイクロフォーカスX線CTシステム、inspeXio SMX-225CT FPD HR Plusを活用することで、サンプルを非破壊かつ接合部全体の連続的な断面観察が可能となり、加工品質の検証には最適です。図3に本装置を示します。図4はΦ1.8mmの純銅単線の突合せ溶接の加工サンプル(図1)のマイクロフォーカスX線CTによる観察結果です。接合部全体にわたってクラックや未接合箇所は存在しないことが確認できます。また図4上部の断面画像が示すようにΦ100μmのボイドが一箇所、さらにΦ数10μmのボイドが複数存在することがわかりました。ボイドは、加工条件を最適化することにより低減が期待できます。
図5はアルミニウム平角線溶接(図2)のCTによる断面画像の一例です。ボイドは確認できず、非常に高品質な溶接ができていることを確認しました。

【 図3 マイクロフォーカスX線CTシステム 】

- 【 図4 Φ1.8mm銅単線溶接のCT画像 】
- 上図:横断面、下図:縦断面
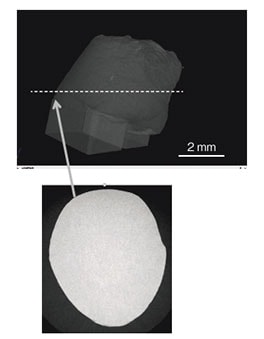
- 【 図5 アルミニウム平角線溶接のCT画像 】
- 上図:三次元表示画像、下図:断面
② レーザ粉体肉盛法(LMD:Laser Metal Deposition)による銅コーティング
次にレーザ粉体肉盛法(LMD:Laser Metal Deposition)によるSUS基板上への銅コーティング例を示します。LMDは母材にレーザを照射しつつ、母材表面に形成された溶融池に金属粉末を供給することで溶融凝固させて堆積する方法です。実験セットアップを図6に示します。従来のLMDは安定した溶融池を形成するために高出力のレーザを必要としましたが、金属粉末を中心部から噴射投入し、円周方向から光吸収率の高い青色半導体レーザを照射して飛行中の金属粉末を母材表面に到達する前に溶融させることで、溶融池の形成を抑制し、低入熱かつ高速なコーティングが可能になります。
加工条件は、青色レーザ出力合計120W、スキャン速度80mm/sです。銅粉末の平均粒径は約30μmであり、噴射投入する粉末の収束径を制御するためのガス流量は3.5L/minです。図7に示す結果の通り、SUS基板上に問題なく銅コーティングができています。
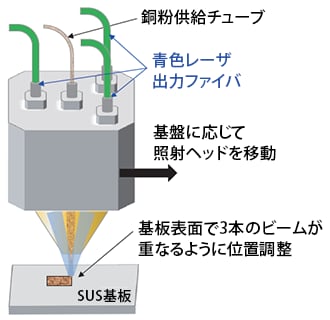
【 図6 レーザコーティング実験のセットアップ 】
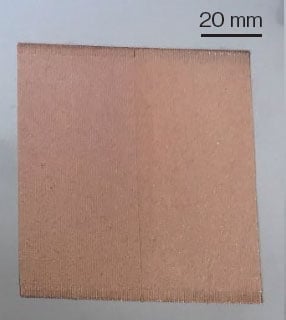
【 図7 SUS基板上への銅コーティング例 】
LMDによりSUS基板上に純銅をコーティングしたサンプルでは、母材金属が溶着金属に溶け込む、いわゆる希釈の程度を正確に分析することが望まれます。島津製作所の電子線マイクロアナライザ(EPMA)は表面分析手法の一つであり、微小領域における元素の種類や重量比率、分布の測定が可能です。図8に島津製作所のEPMA-8050Gと主な仕様を示します。
Item | Performance |
---|---|
形態観察 | 40~100000倍程度 |
測定元素範囲 | Be(原子番号:4) ~U(原子番号:92) |
分析深さ | 表面から数μm |
搭載可能 サンプルサイズ |
100×100×H50mm |
搭載可能 サンプル重量 |
2kg(耐真空、導電性要) |
【 図8 EPMA-8050Gと主な仕様 】
図9は、EPMAによる純銅コーティングした加工サンプル(図7)の分析結果です。SUSの含有を調べるためにFeのKα線を利用しました。一つの断面でFe(Kα)、Cu(Kα)を測定し、鉄と銅の二次元元素マッピングを実施しています。図9の結果より鉄と銅が比較的分離しており、表面部はほぼ銅であることがわかります。
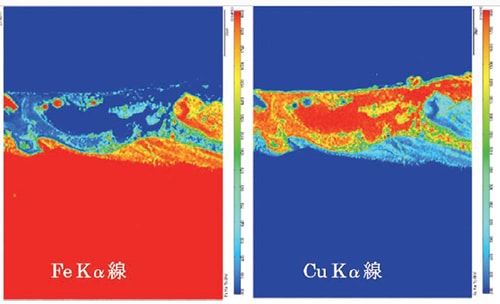
【 図9 EPMAによる純銅コーティングサンプルの元素マッピング 】
プロセスインフォマティクスと青色半導体レーザ光源で生産技術改革へ貢献へ
本稿で紹介した青色半導体レーザによる加工プロセスでは今後マイクロフォーカスX線CTや電子線マイクロアナライザの結果をフィードバックし、ボイドの低減や異種金属の溶け込みを最適化する必要があります。加えて、他の分析計測装置(万能試験機、高速ビデオカメラ、レーザスペクトルアナライザなど)を組み合わせて加工品質を検証した解析結果を蓄積し、最適な加工プロセスを事前に予測するプロセスインフォマティクスへの展開が期待されます。これにより、課題である生産技術改革に対しスピーディにソリューションを提案し、レーザ加工用光源として青色半導体レーザ光源のデファクトスタンダード化を目指していきます。