※本稿は株式会社KRI様からの寄稿です。
株式会社KRIスマートマテリアル研究センターについて(外部サイト)
クルマの電動化、自動運転化やコネクテッド化によって、車載される電子機器は各段に増えています。さらに、高電圧化も進んでおり、車載電子機器の熱対策はますます重要になっています。
Thermal Interface Material(TIM)とは、電子機器の内部で発生した不要な熱を効率よく放熱するために部材間に挿入される熱伝導性材料のことです。基本的にはシリコーンやエポキシなどの樹脂中に高熱伝導フィラーを高充填してシートとしての熱伝導性を向上させています。現在ではスマートフォンや各種電子機器のみならず、ハイブリッド自動車や電気自動車のモーターを駆動するインバーター等様々な分野で利用されています。
例えば、電子機器に搭載されるCPU(Central Processing Unit)は、素子の上に絶縁性のTIMと金属製の放熱フィンを配して素子を冷却します(図1)。チップの放熱性が期待通り発揮されない原因としては、TIM内部のボイド、素子との貼り合わせ時のクラックやボイド、部材の熱膨張差による剥離等によって界面熱抵抗が発生していることが考えられます。また、前述の様にTIMにはフィラーが高充填されているため、樹脂とフィラー界面にボイドやクラックが発生すると、その部分が熱抵抗になることも十分に起こり得ます。このようにCPUの冷却性能は、その冷却構造だけでなく、TIMの内部構造も熱伝導材料としての性能を左右する重要なパラメーターとなり得ます。したがって、材料中の構造を把握し問題点を明確化することは重要となります。
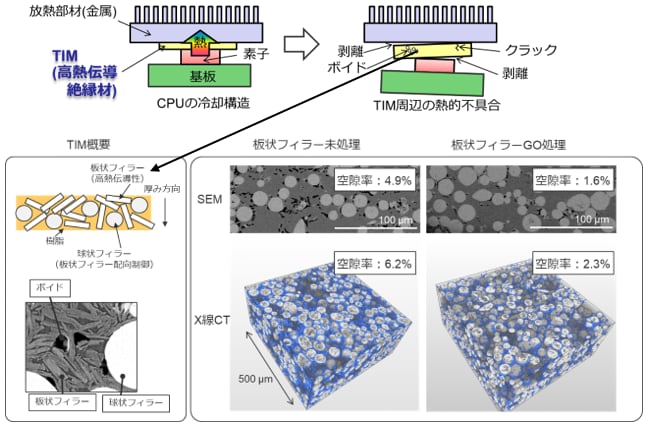
【 図1 CPUの冷却構造と不具合の発生状態およびTIM内部の構造とボイド観察結果 】
今回、TIMの内部構造を走査型電子顕微鏡法(Scanning Electron Microscopy, SEM)とX線CTを用いて評価し、ボイドなどの空隙情報が3次元的にも広がっていることを確認することができましたので、紹介します。
材料開発では分析評価によるフィードバックが重要
材料開発現場では、構成する要素材料を含めて材料をよく理解しハンドリングする事と同時に、材料そのものを評価し結果を開発へフィードバックする事が重要であり、通常、開発と分析評価は互いに協奏が必要な取組と言えます。
受託研究を主事業としたKRIは、材料の研究開発、材料分析、技術調査において数多くの技術蓄積があります。TIMに関わる分野においては、絶縁性の炭素材料(酸化グラフェン:GO)をフィラーに吸着させ、熱伝導率を向上させる技術を保有しています(図2)。これは、表面の官能基が少なく、これまで表面処理が難しいといわれていた六方晶窒化ホウ素(h-BN)の表面にGOが吸着する現象を利用して表面処理を行うことで実現しています。熱伝導率向上の理由の一つとして、GOを介することによって樹脂とh-BN界面の親和性が向上し、ボイドやクラックが発生しにくくなることが考えられます。
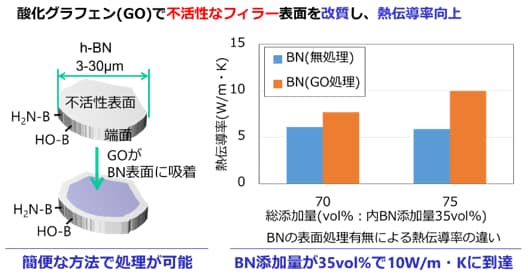
【 図2 h-BNへのGO処理の概略と熱伝導率の向上事例 】
材料の構造評価は複数手法の組み合わせ
材料の構造観察に広く用いられる方法としてSEMやX線CTがあり、それぞれに長所と短所があります(表1)。
評価方法 | 長所 | 短所 |
---|---|---|
SEM | nmサイズの構造評価が可能 | 三次元構造の把握は困難 |
X線CT | 三次元構造の可視化が可能 非破壊での検査が可能 |
nmサイズの構造評価は困難 |
例えば、SEM観察ではnmスケールの微細な観察は可能ですが、1断面のみの観察であるため材料の三次元構造を把握する事は困難です(図3)。材料の内部構造を正確に把握するには、それら手法の特徴を十分に理解した上で複数の手法を組み合わせて評価する事が重要になります。
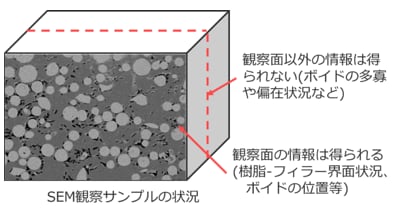
【 図3 SEM観察サンプルの状況と得られる情報 】
材料内部の構成材料の分布の可視化
本検討では、エポキシ樹脂中に板状のフィラーと球状のフィラーを高充填し、プレスで約200μmにシート化したものをサンプルとして用いました。TIM内部を把握するため、試料断面のSEM観察を行ったところ、GO未処理フィラー、GO処理フィラーのいずれの試料においてもボイドが存在していますが、GO処理フィラーを用いたTIM内部のボイド量は、GO未処理フィラーのボイド量に比べ減少している傾向が観察されました(図4)。
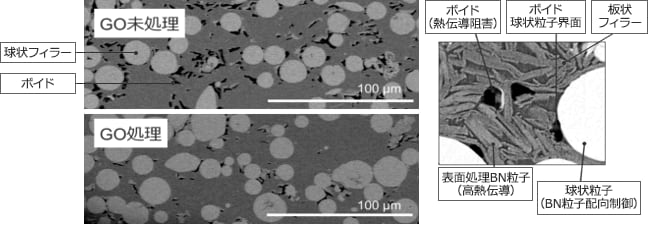
【 図4 TIMの断面SEM観察とボイドの発生状況 】
GO処理によって減少したボイドの定量評価
SEM観察によってボイド量の違いが明らかになったので、ボイド量を定量的に把握するためX線CT観察、およびボイドの定量評価を行いました。図5では、ボイドを青、球状フィラーを白、板状フィラーと樹脂部分を半透明で示しています。GO未処理と比べて、GO処理は明らかに青色の部分が減っていることが分かります。このようにX線CTにおいてもGO処理の効果を明らかにすることができました。
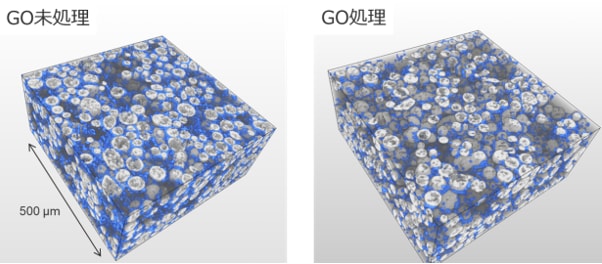
【 図5 X線CT画像とボイドの可視化 】
さらに得られた三次元画像からボイドの体積比を算出したところ、GO処理したサンプル全体のボイド量は2.3%と、GO未処理の場合の6.2%から低減していることが分かりました。この減少傾向は先のSEM観察結果に一致します。
図4のSEM画像と図5のX線CT画像それぞれから算出されるボイド量の計算結果を比較したところ(表2)、SEM画像とX線CT像でGO未処理とGO処理のボイドの差は同程度となりました。若干の数値の違いはSEM画像が一断面での観察であるため、統計量の違いによるものと考えられます。このように、構造評価は複数の観察方法によってクロスチェックを行う事が重要です。
評価方法 | GO未処理 | GO処理 |
---|---|---|
SEM | 4.9% | 1.6% |
X線CT | 6.2% | 2.3% |
解析方法の展開
~フィラーごとのボイド発生状況の明確化
ここまでは、ボイドの存在を確認するにすぎませんでした。材料の熱伝導性向上のためには、フィラー界面のボイドを低減することが重要となります。そこで、ボイドがどのフィラー界面に発生しているかをX線CTで得た三次元画像中で区別し、色分けしました(図6)。このような解析を行うことによって、熱伝導を阻害するボイドがどのフィラー界面に存在するのか、さらにはどのフィラー表面を重点的に改良する必要があるのかが明確になり、改善指針を立てやすくなることが期待できます。
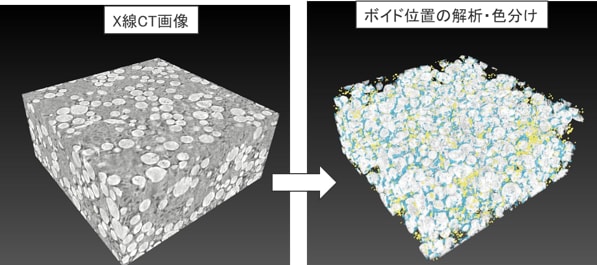
【 図6 X線CT画像とボイドの可視化。
ボイドを青、球状フィラーを白、板状フィラーと樹脂部分を半透明で示す。 】
このように、高熱伝導性材料において、X線CTを用いて樹脂とフィラー界面のボイドやクラックを定量的かつ視覚的にとらえる事に成功し、熱伝導率向上に役立てることができました。本評価で使用した手法は様々な成型品やアセンブリーした部品などでも応用できると考えられ、熱伝導性や電気特性等の不具合の原因や個所の特定に大きな効果が期待できます。
- ※本稿は株式会社KRI様からの寄稿です。
- ※本稿に関連するお問い合せについては、一次的には株式会社島津製作所にて承りますが、内容によっては、お客様のご了解を得た上で株式会社KRIと共同で対応させていただく可能性がございます。