急速に進む世界的なEV(電気自動車)へのシフトやカーボンニュートラルへの対応、CASEへの対応のため、自動車関連メーカーは様々なテーマの開発を迅速に進めなければならなくなっています。
自動車開発の効率化、迅速化のため、MBD(Model Based Development)が広まっています。MBDでは、CAE(Computer Aided Engineering)が活用され、シミュレーションで様々な性能の検証が進められます。シミュレーションが、リアルな試作検討に取って代わり、費用や開発期間を大幅に削減、短縮する等、開発方法は大きな変革の中にあります。そのようなシミュレーションを実測で検証することが必要となっています。
本稿では、CAEによるシミュレーション結果の検証と妥当性確認、いわゆるV&V(Verification & Validation)に活用できる新たな計測技術として、3D-DIC解析とin-situ X線CTによるDVC解析を紹介します。
シミュレーションを高精度化するために
自動車部品設計においてもCAEの活用は広まっています。しかし、特に、弾性領域を超え、永久ひずみ、損傷・破壊を伴うCAEの場合では、計算結果と実測結果には多くの場合乖離があります。そのため、CAEには、材料特性の代表的な値に加え「応力ひずみ線図」などの高度な材料情報を用いて解析モデルが実物と合うよう、モデルを作り上げ、モデル精度を向上させることが重要となります。
モデルの高精度化には実測に基づく計算パラメータの調整が必要となりますが、従来の材料分析で得られるデータだけではモデルと実測の乖離要因を理解することができませんでした。その結果、曖昧な部分は安全マージンを多めに取る設計をしなければならず、それはコストや部品重量の増加につながってしまいます。モデルの高精度化、その結果として設計を最適化するには、材料が変形、破壊するメカニズムを可視化し、理解できることが必要となります。それによって、設計上重点的に手当てすべき箇所が分かり、必要以上の安全マージンをなくすことができます。
そこで、材料の物性試験をしながらその様子を画像観察することで、破壊のメカニズムを可視化する二つの技術を紹介します。
本掲載技術は、株式会社島津テクノリサーチにて提供している受託分析での試験サービスとなっています。
デジタル画像相関法(DIC:Digital Image Correlation)と応力三軸度の計測
通常の材料分析(引張、圧縮、曲げ)では、素材がどのくらいの力でどのくらい伸びたか、どのくらいの力をかけたときに破断したか、という数値データしか得ることができません。これに対し、デジタル画像相関法では、材料分析と同時に画像観察を行い解析することで、「ひずみ分布」「応力集中部」のデータを得ることができます。
この手法では、試験片表面の模様(元々ある模様や、塗料等で作成したものを使います)が、力を加えられたときに起こる変形の画像変化をカメラにて捉え、解析することで、視野全体の変位・ひずみ分布データを取得します。このため、ひずみゲージでは、計測の難しい連続的なひずみ分布の評価が可能となるのみならず、ゲージの方向も後から選べる等、画像相関法は複雑な変形・損傷の評価において効率的にデータ収集が行えます。
従来の一軸引張時のデータのみでの判断では無く、応力3軸度域での破壊挙動を計測し、3D-DIC解析で、ひずみ分布を得る手法です(図1,図2)。
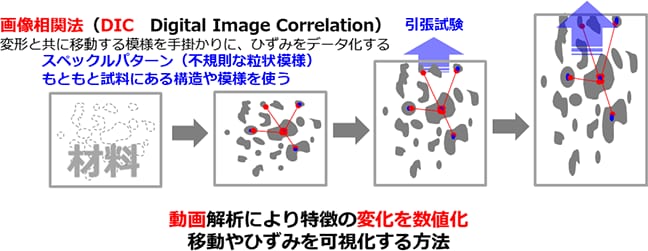
【 図1 画像相関法のイメージ図 】
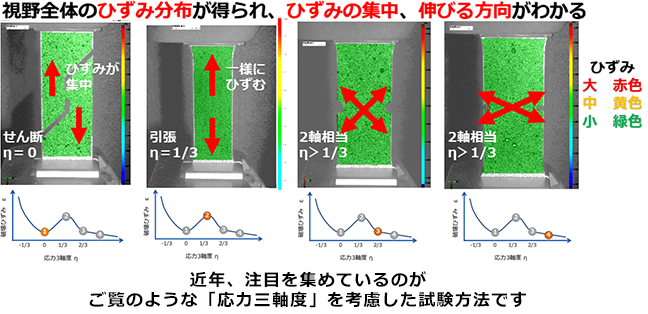
【 図2 応力3軸度域での計測で得られる「ひずみ分布」 】
島津テクノリサーチの3D-DIC解析の特長
「高速撮影が可能」
島津製作所が製品化した世界最速レベルの高速度ビデオカメラ(Hyper Vision)を使用することで、試験時の破壊における細かい挙動をマイクロ秒間隔で確認できます。
「さまざまな温度環境下での試験が可能」
自動車が走行する地域の広さから、部品には温度や湿度等、幅広い環境条件での特性の把握が必要です。このため、温度範囲-40℃〜150℃の環境下での試験を可能としています。
デジタル容積相関法(DVC:Digital Volume Correlation)と、in-situ X線CT
DIC解析は、カメラ画像を基にするため材料の表面のひずみが計測の対象でした。一方、DVC解析では、X線CTを使うことにより試験片の表面のみならず、材料内部、すなわち全体が計測の対象となります。外部より力が加わって変形する試験片の内部の画像変化が、X線CTで動的(in-situ X線CT)にとらえられます。島津テクノリサーチでは、X線CTでの観察用の試験機器を独自開発しています。
計測・解析の手法はDICと同様、試験片内部の組織等(模様に相当)を手掛かりに、視野全体の「変位・ひずみの分布」や「応力集中部」を特定できます。また、in-situ X線CTの観察機能を活用し、力が加わる状態で得られる多様な画像データの解析も可能です(図3)。
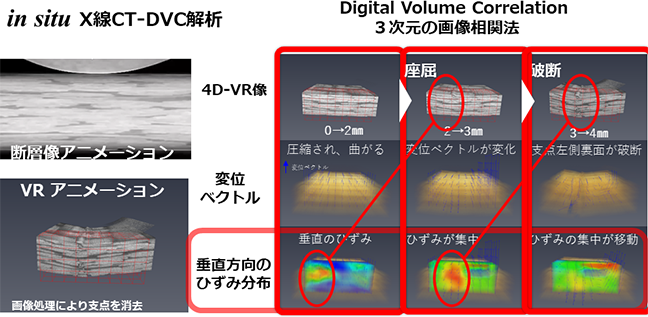
【 図3 試験片が破断に至るまで、in situ X線CTで撮影、再構成した3次元像で捉えています。
これをDVC解析しデータを得ます。 】
島津テクノリサーチのin-situ X線CT観察の特長
In-situ撮像に適した[X線CT内で設置できる試験装置]を自社開発し、
高画質なデータを取得
装置の試験力容量として、現状、サイズの異なる100N、2kN、5kN、20kNを用意しており、100Nの小型タイプは幅数ミリ角程度、長さ15mm程度まで、2kN、5kN、20kNのタイプは、およそ幅20mm程度、長さ約150mm程度(推奨75mm程度)までに対応しています。
特許出願の特殊構造により、試験機本体は小型サイズながらも、大きな試験空間を実現し、突き刺し試験治具や、せん断試験治具等のような、各種のご要望にお応えするために様々な特殊治具開発等の対応も行っています(図4,図5)。
なお、2kN、5kN、20kNタイプは、専用特殊3点曲げ治具による曲げ試験に対応しており、特許出願の傾斜機構により、3点曲げ試験においてもアーチファクトを低減したCT撮影が可能です。
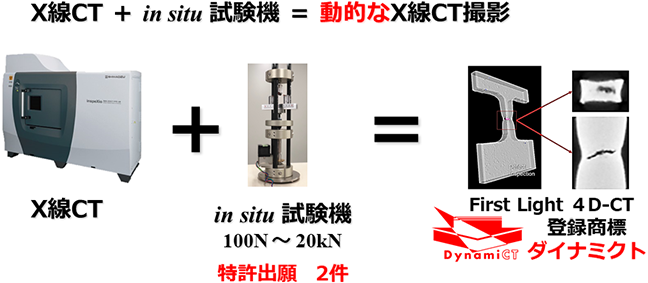
【 図4 X線CTと、CT内に設置できる試験機です。これにより破断に至る過程が計測できます。 】
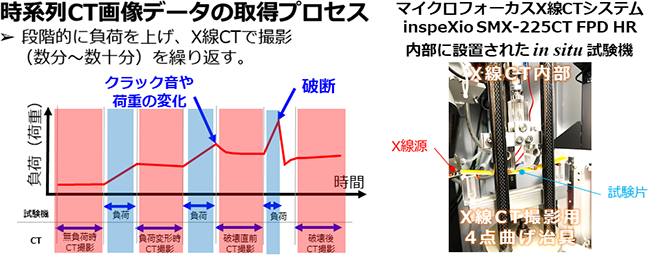
【 図5 動的なX線CTの計測プロセスを示します。写真はX線CT内に設置されたin situ 試験機です。 】
シミュレーションとの連携:「応力ひずみ線図」
CAE担当者が必要とする「応力ひずみ線図」に、実測データを基にした、新たな解釈や補正を加えるための手段が充実してきました。DIC解析の得意とする高速な破壊現象の確認、そして弾性域領域はもちろん、in-situ X線CT撮影およびDVC解析によって、初期の内部損傷、き裂、破壊の進展について、より詳細な知見を得ることが可能になります(図6)。
これらにより、従来はあいまいなままに決定せざるを得なかった一部のCAE解析条件に対し、実測データを根拠として織り込んだ、より信頼性の高いCAEの解析条件の最適化や、従来にはみられなかった多角的な実測データに基づくValidation&Verificationにお役立てください。
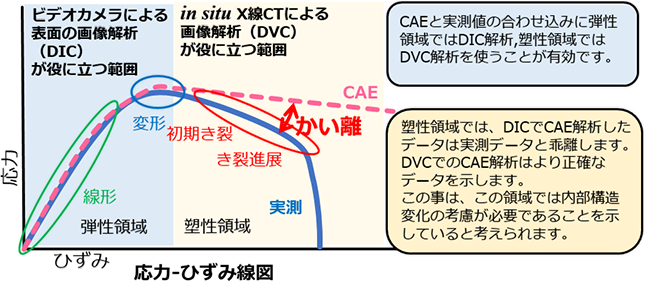
【 図6 DIC、DVCを活用し、CAEに必要な正確な「応力ひずみ線図」を得ることができます。 】
※島津グループでは「試験システム」の提供と同時に、島津テクノリサーチにて受託分析も行っております。お客様では手のかかる、特殊な計測方法・解析技術・試験技量が必要な分析・計測や、目的に特化した計測機器も用意し、必要なデータを提供しております。
分析・測定・調査の株式会社島津テクノリサーチ (shimadzu-techno.co.jp)