自動車の動力源が、エンジンから電動モータに変わることで、「熱の問題」が大きく変化しています。大量に搭載されるバッテリーは温度の影響を受けやすく、10~40℃内に制御する必要があると言われています。電気自動車では、熱を捨てるのではなく再利用する、利用効率を上げる等を狙いとして、発生・消費する熱を車内全体で最適化するための制御機構(サーマル・マネージメント・システム/エネルギー・マネージメント・システム/熱マネジメント・システム)の開発・実用化が多くの企業で始まっています。
新たな発熱源から効率よく放熱し、必要なところへ届けるための課題
「熱源からの放熱」には、熱源が高温化し破損することを防ぐ目的もあり、効率的な方法が必要です。電気自動車での熱源は、モータ・インバータ等で、エンジンに比べ小さな部品となっています。そうした密集する電子部品では発生した熱を取り出す放熱部分が大きくできず、単位面積あたりの吸熱量を大きくする必要があります。
電子部品の搭載数は増加傾向で、インバータを構成するパワーモジュールは「モータの高回転化、高トルク化」や「電池充電時間の短縮」といった効果を目指し「駆動電圧の高電圧化」が進んでいます。発生熱量は、今後増加する方向となっています。
熱の課題に立ち向かう、サーマル・マネージメント・システムは多様な技術要素で構成されますが、「熱を効率よく取り出す」「取り出した熱を輸送する」ことに特長を持つ、島津の「二相流体熱輸送技術」を紹介します。
不要な熱を必要なところへ届ける二相流体熱輸送システム
通常の熱輸送には、液体の温度変化による熱移動(顕熱)を利用する『液冷方式』が用いられていますが、島津製作所では冷媒が気体から液体、あるいは液体から気体に相変化する際の熱移動(潜熱)を利用する『二相方式』のシステムを開発しました。
潜熱は顕熱と比較して熱移動性能が著しく大きいという特性を利用し、『二相方式』は「液冷方式」に比べ、非常に大きな熱を熱源から奪うことができます。実際にスーパーコンピュータ等の放熱技術では「液冷」に比べ数倍~10倍に近い性能増が期待されています。
では、『二相方式』の構成を説明します。図1に示される冷媒の循環システムの中で、冷媒は液体⇔気液二相と変化します。先ず、ポンプ(B)で押し出された液体冷媒は、熱源と接する蒸発器(C)で、液体→「気液二相」へ変化しながら熱源の熱を受け取ります。熱を受け取り気液二相となった冷媒は、気液二相管(D)を流れ、凝縮器(E)で、ヒートシンクに熱を放出することで液体に戻り、液管(F)を流れ、液溜(A)を経て、ポンプ(B)へ循環します。
例えば電気自動車のモータや電池、インバータ部分に蒸発器を設置し、自動車のシート部分にヒートシンクを設置すれば、発生した熱をシートヒータとして利用できる可能性があります。
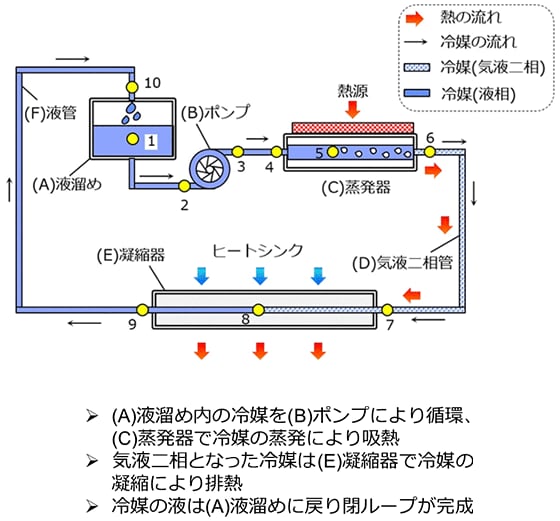
【 図1 二相流体熱輸送システムの仕組み 】
二相流体システムが、従来の液冷システムより優れる性能
『二相方式』は「液冷方式」と比較し、以下の点で優れています。
- ①システム自体を小型・軽量化・省エネルギーで運転することが可能になります。
- ②単位面積当たりの吸熱量が大きく、小さな範囲で発熱量が大きい電子部品の冷却・排熱利用に適していると考えられます。
- ③蒸発中の冷媒温度はほぼ変化しないため、蒸発器内の温度均一性に優れています。「液冷」では吸熱する過程で温度が上がるため、冷媒の入口部より出口部の温度が上がり、吸熱能力が低下します。
二相流体熱輸送システムに求められる高度な制御技術
このように様々なメリットが考えられる二相流体熱輸送システムですが、理論的には以前から検討されていたものの、システムの安定稼働に課題がありこれまであまり実用化されてきませんでした。
二相流体熱輸送システムの弱点は、冷媒の沸点に近い温度帯で稼働させることから、冷媒が液体であるべき箇所で気体になったり、気体であるべき箇所で液体になったりという誤動作が起こりやすくなる点です。これが、蒸発器中で冷媒がすべて蒸発し吸熱できない“ドライアウト”の発生や、ポンプ故障の原因となり、システムの安定運用が困難でした。
島津製作所では、ドライアウトの予兆を検知して回避できる機器構成と制御則や、ポンプに気体が混入しない(液体を確実に供給する)ための機構を構築し、このシステムに最適な高度な気液二相の制御技術を確立することで、これらの課題を乗り越えるシステムを実現しています。
航空機基準で開発された高い耐環境性と堅牢性
島津製作所では、二相流体熱輸送システムを航空機に搭載することを目指し開発を進めていました。長年航空機向けに開発してきた多くのシステムで蓄積してきたノウハウを使い、小型軽量に加え、航空機での使用に耐えられる耐環境性、堅牢性を持った材料や構造を採用しています。
これらの実績を基礎に、自動車をはじめとした様々なモビリティへの搭載への展開を検討しています。